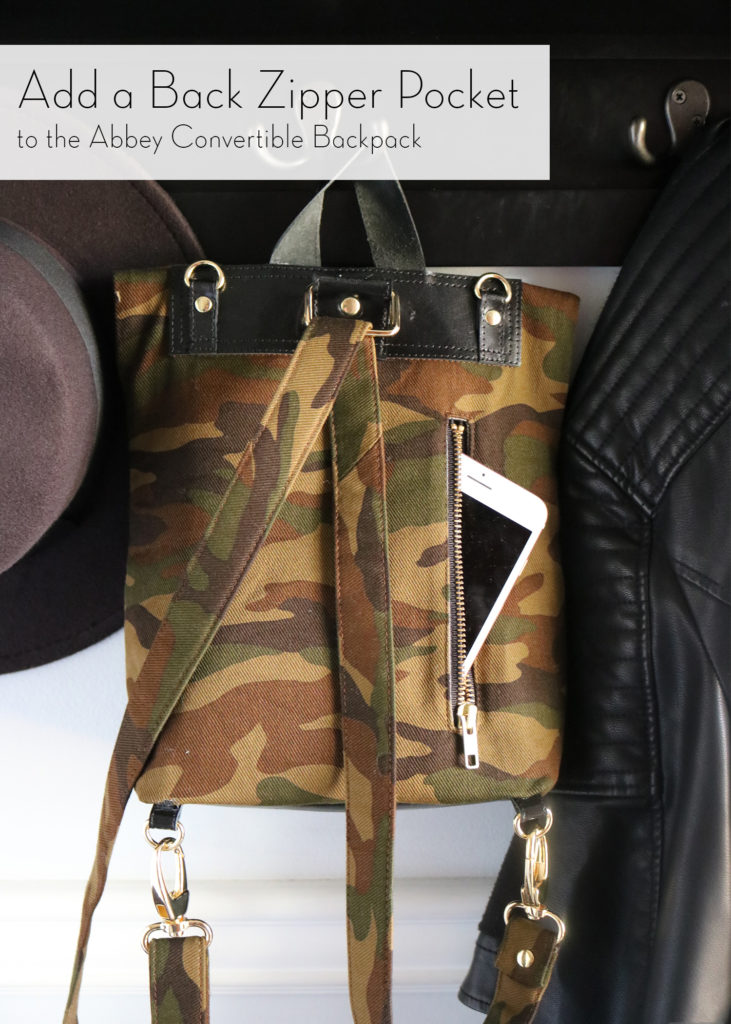
The Abbey Convertible Backpack is my go-to bag when taking day-trips with my kids. I like having it out of the way but still being able to hold the essentials. But being a designer, I constantly have new ideas and wish there were different features with every bag I own.
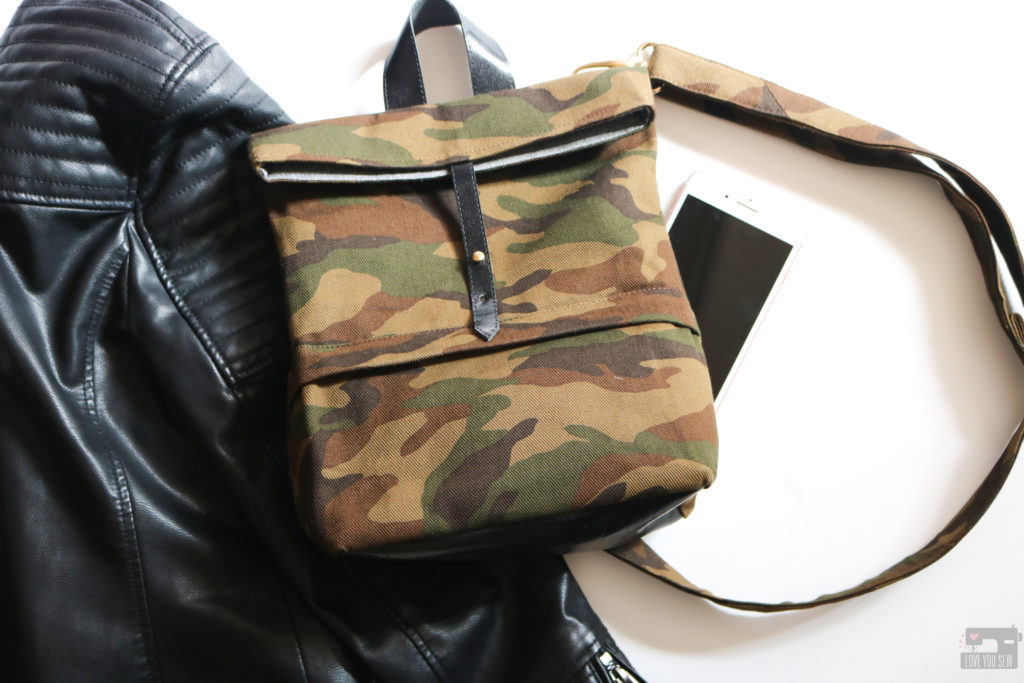
On the back of the Abbey, there is a slip pocket. I added the feature with the intention that it would be a quick spot to hold your phone or keys without having to open the main compartment as frequently. But since I happen to wear my bag more as a backpack, I have to swing it around to access the pocket and felt that a slip pocket just isn’t as secure for an expensive smartphone — and BOOM, I have the idea for the back welt pocket hack.
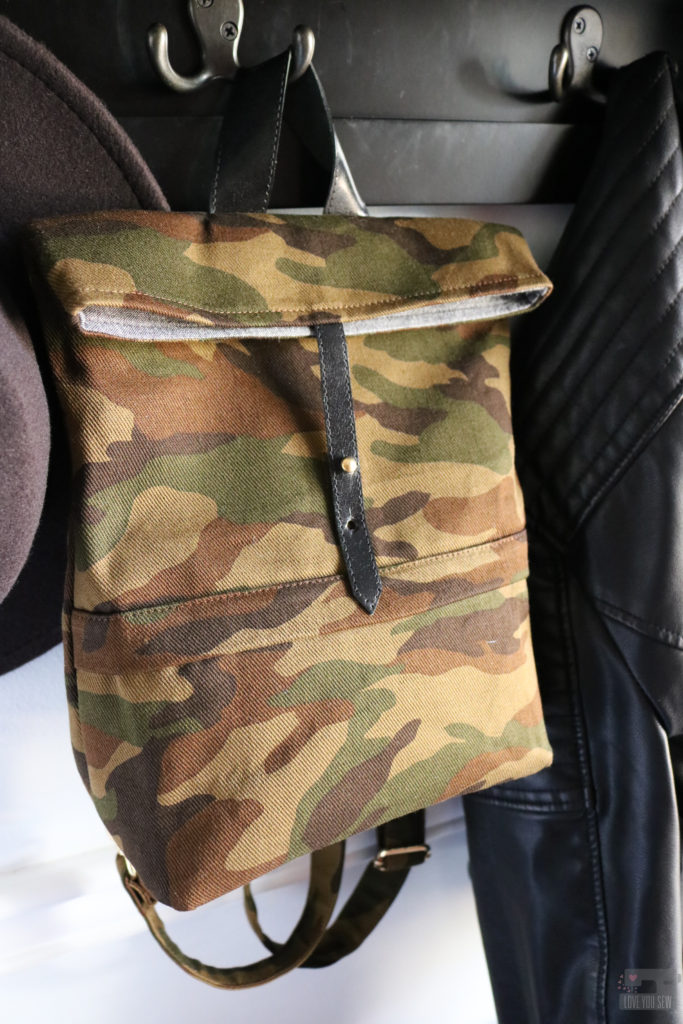
Back Welt Pocket Tutorial
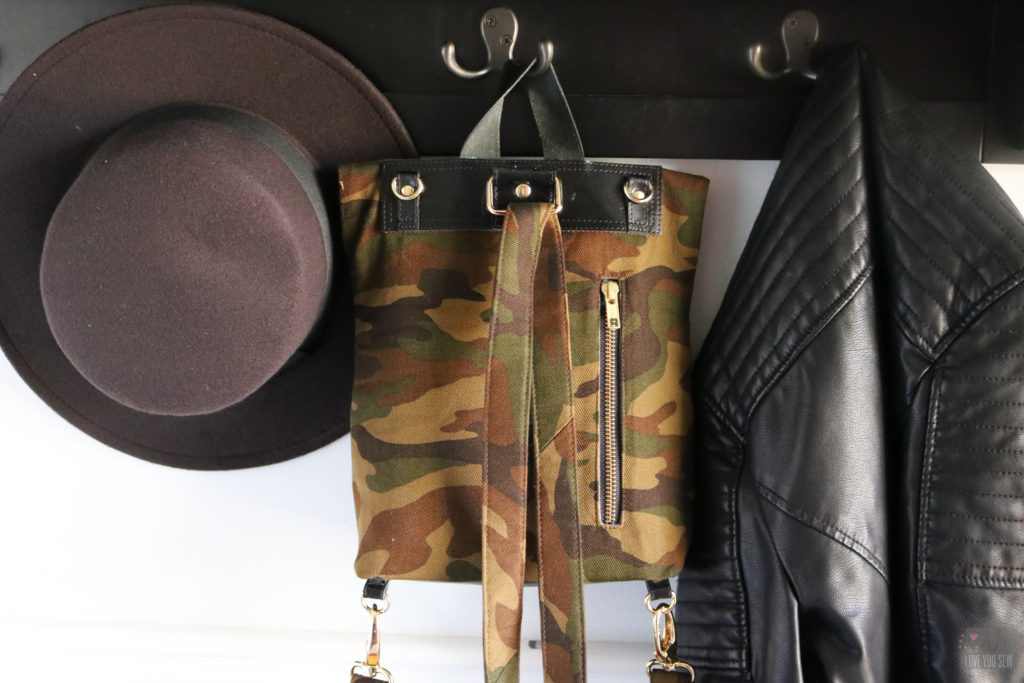
You will need the original instructions and templates for the Abbey Convertible Backpack which you can find here. Additionally you will need:
- 6″ Zipper
- 8 3/4″ x 12″ Lining Fabric + Interfacing (this is large enough to fit an iPhone 7+ with a thick Otterbox case.)
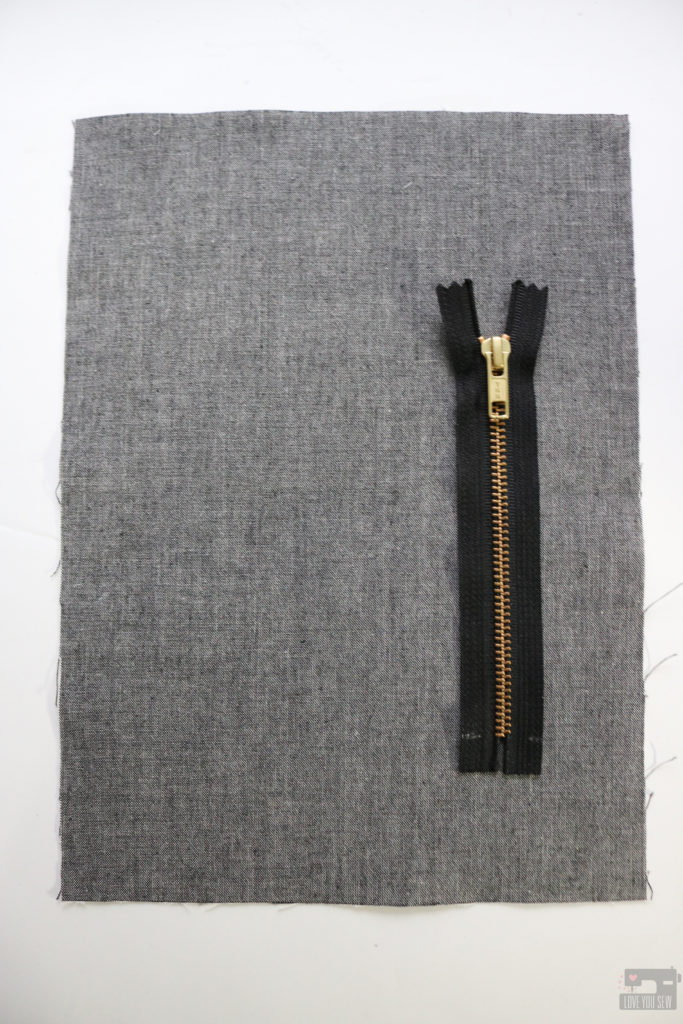
To make the Back Zipper pocket, you will omit all of the fabric and interfacing for the Slip Pocket and move through Step #41. (Please note I don’t have connectors added to my handle base at this point since I used leather and added them later.)
Draw a rectangle measuring 6″ x 1/2″on the wrong side of the Pocket Lining centered and parallel to the short side as shown. The Zipper will run vertically. There should be 1 3/8″ above and below the rectangle and 3/4″ space to the right.
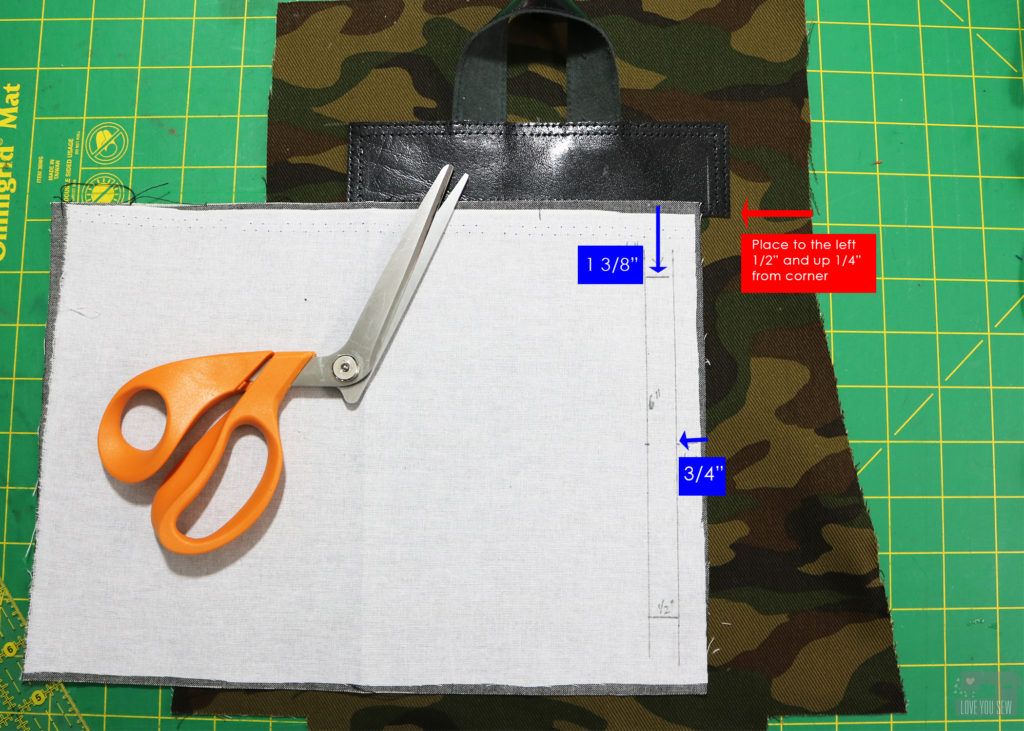
Line up the Pocket Lining as shown with the right edge 1/2″ in and up 1/4″ from the sides of the Handle Base. Pin the Pocket Lining in place. Go back and follow Steps #21-28 to finish the pocket! Voila – a chic looking vertical zipper pocket to keep your phone or other valuables a little more safe as you sling the backpack around.
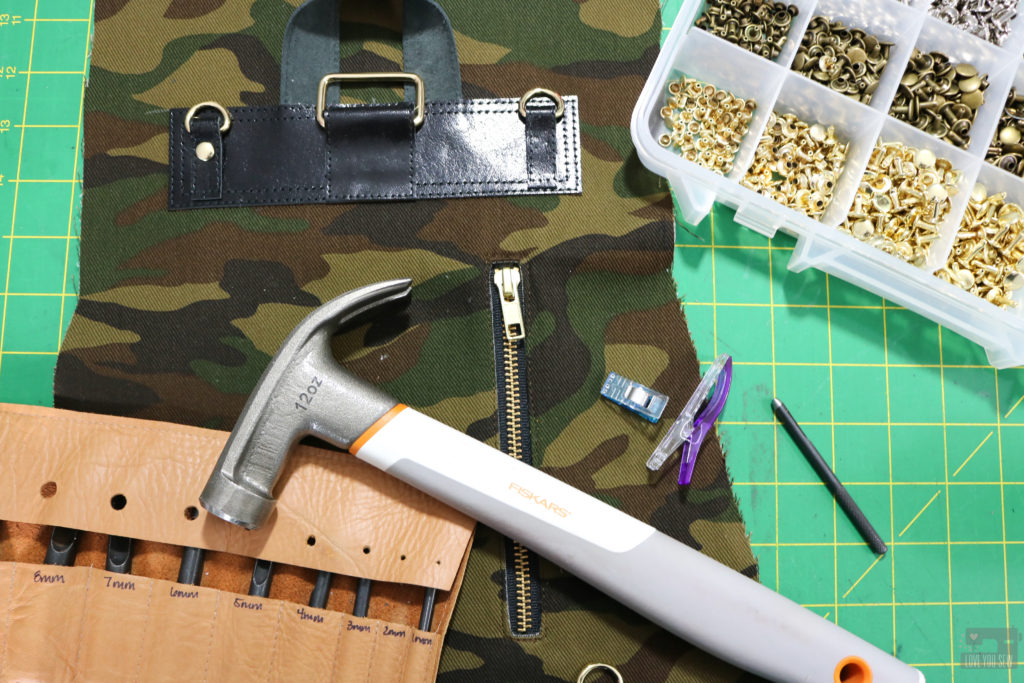
Since the Pocket Lining hangs vertically instead of horizontally, the weight of a phone would make it drag awkwardly and pull on the zipper. So, the Pocket Lining needs to be anchored horizontally so the weight can hang straight down naturally. To do this, flip the back of the bag right side up and sew directly below the Handle Base from corner to corner catching the Pocket Lining. Back-stitch well.
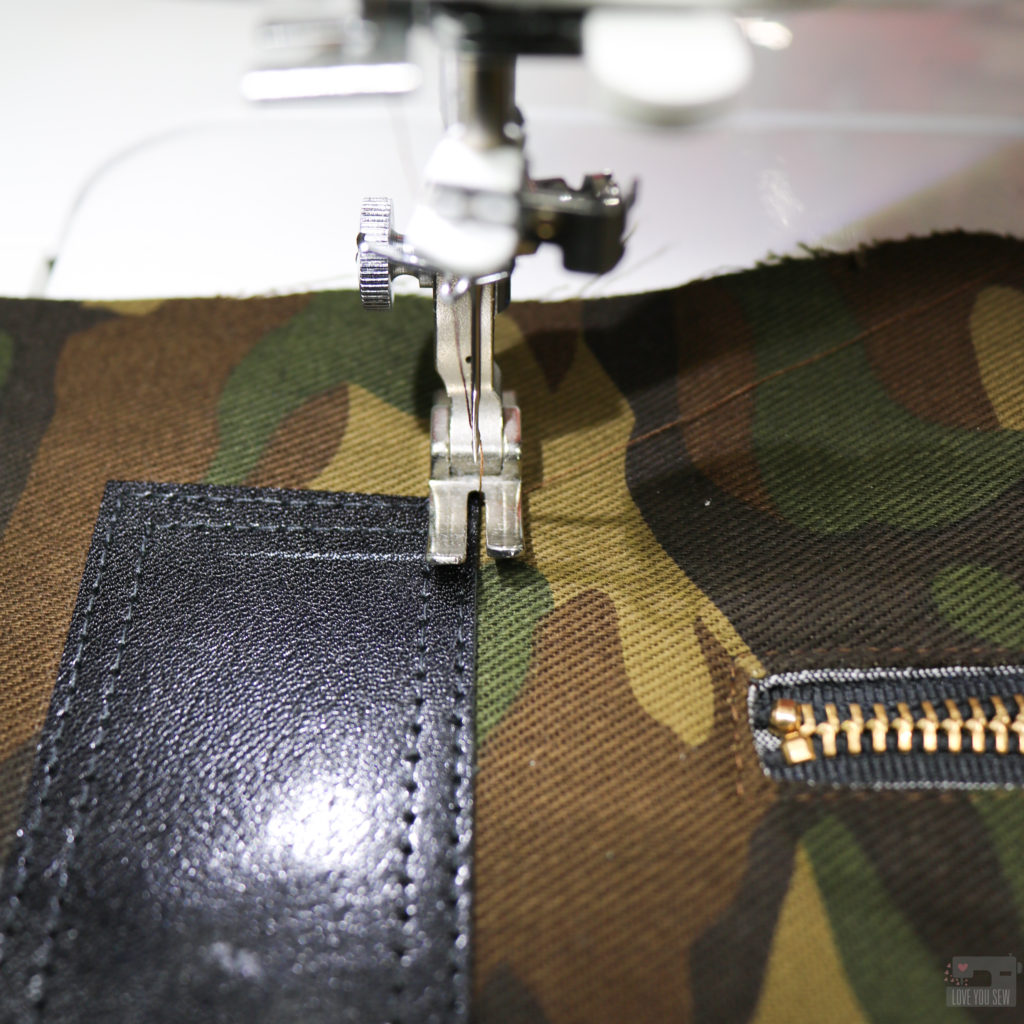
This is the wrong side after securing the Pocket Lining. The weight of the phone is evenly distributed and won’t distort the structure of the bag.
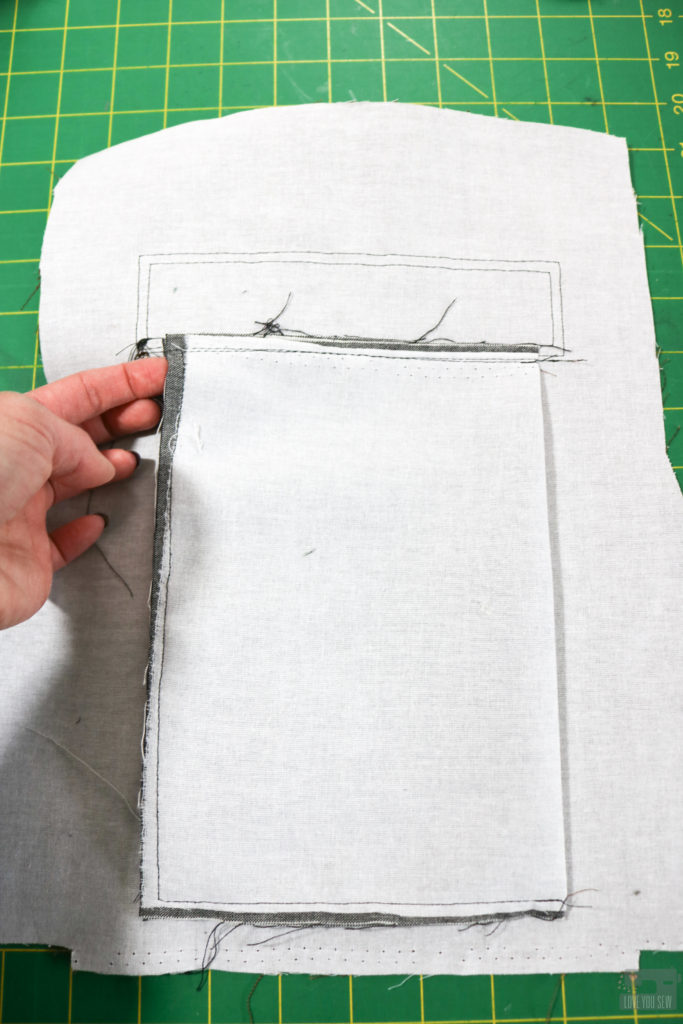
Additional Modifications
You know I cannot resist using leather in my personal bags! I had this great glazed black upholstery leather I got from Tandy which I used to make a few Kelly Waist Bags. The scraps are great for all of Abbey’s accents like the connectors, handle and closure tab.
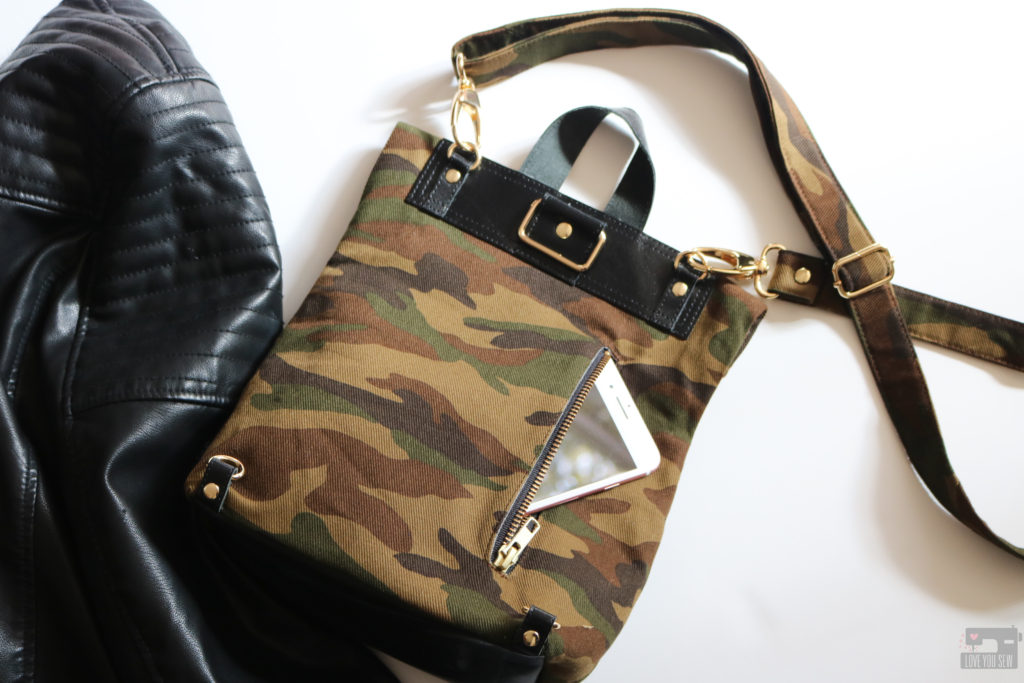
I also used my other Abbey Backpack Zipper Cover and Button Stud Hacks which you can find here. I like the clean look from the front and just love using button studs with leather.
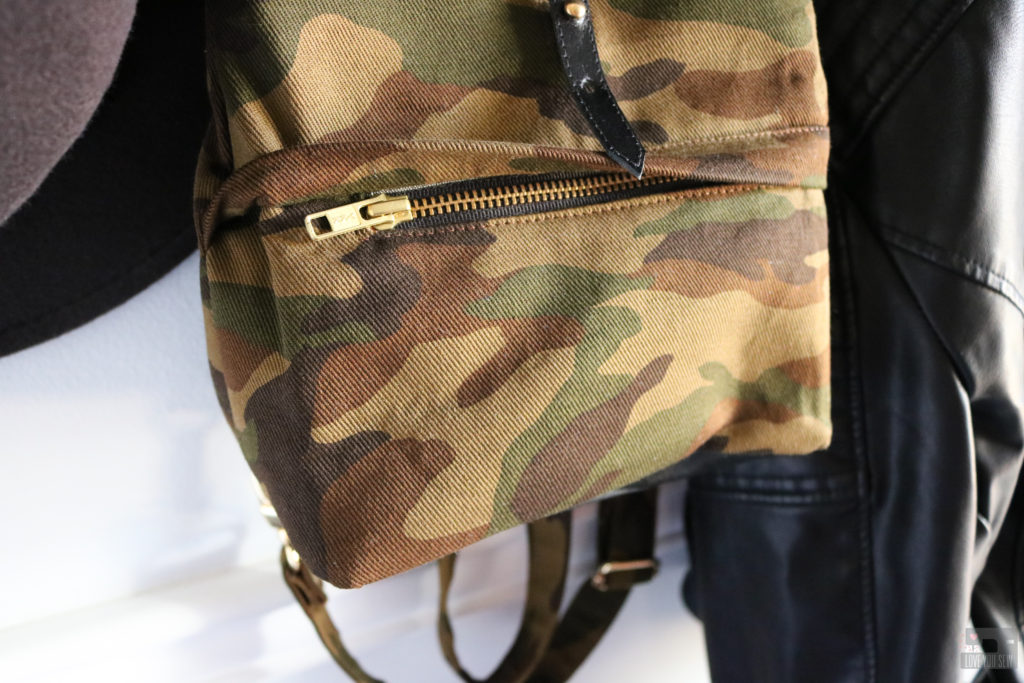
Project Details
- Fabric: Camouflage Twill Canvas by Sevenberry for Robert Kaufman (aff link)
- Lining: Essex Linen by Robert Kaufman (aff link)
- Zippers: YKK #5 Metal from Wawak
- Hardware: Emmaline Bags
- 3Leather: Upholstery overstock from Tandy Leather
- 6mm Button Stud (aff link)
- Interfacing: Pellon SF101 (aff link)
I hope you enjoy this hack and even use it for other projects! Don’t forget to use #abbeyconvertiblebackpack and #loveyousewpatterns on social media so everyone can see your fabulous makes!
Hugs and Stitches,
Cristy
This post may contain affiliate links which I use to keep this website pumping along. Please visit my Disclosures page for all the info on my affiliate relationships.